Wytłaczarki Laboratoryjne LE-2CC 2x20 mm oraz LE-2CC 2x24 mm (co-rotating and counter-rotating extruder).
Odwzorowanie, projektowanie i skalowania procesów wytłaczania przemysłowego w warunkach laboratorium badawczego.
Ze względu na wysoką złożoność procesu wytłaczania, wytłaczarka laboratoryjna pomimo niewielkich gabarytów powinna mieć możliwość odwzorowania wszystkich możliwości wytłaczarek przemysłowych. Ponieważ wytłaczarki laboratoryjne niejako wybiegają w przyszłość powinny przewyższać przemysłowe pod względem wyposażenia i funkcjonalności. Jest to ważna kwestia, ponieważ od wytłaczarki laboratoryjnej wymagamy, aby mogła służyć do opracowania nowych jeszcze nie znanych kompozycji polimerowych. Użytkownik oczekuje, że szybko i sprawnie przygotuje wytłaczarkę do kolejnego zadania badawczego nawet kilka razy w ciągu dnia. Od wytłaczarki przemysłowej nie wymagamy tak szybkich zmian. Aby osiągnąć ten cel wytłaczarka laboratoryjna musi szybko nagrzewać i chłodzić strefy cylindra w celu maksymalnego skrócenia czasu poświęcanego na oczekiwanie na zmianę parametrów. Konieczna jest dostępność bogatego wyposażenia takiego jak różne konfiguracje cylindrów i ślimaków, dozowników (proszków, granulek, płynów), dozowników bocznych oraz systemów pomiarowych ciśnienia, temperatury, sił działających na ślimaki oraz innych. Ważna jest kwestia możliwości szybkiego otwarcia cylindra oraz ułatwienia czyszczenia. Zmniejszenie skali maszyny w połączeniu z wszechstronnymi możliwościami, dostosowaniem do prawie każdego zadania i łatwą obsługą systemu stanowią wyróżnik wytłaczarek laboratoryjnych. Wytłaczarki laboratoryjne są doskonałym instrumentem przeznaczonym do badań.
Głębokości kanału w wytłaczarce dwuślimakowej.
Wytłaczarki dwuślimakowe (TSE) używają segmentowych ślimaków zmontowanych na wale. Wał ślimaków przenosi wysoki moment obrotowy. Cylindry wytłaczarek dwuślimakowych również posiadają konstrukcje segmentową i są wyposażone w wydajne systemy ogrzewania i chłodzenia. Silnik wytłaczarki dostarcza energię mechaniczną do stopu poprzez obracanie ślimaków. Część energii mechanicznej zostanie zamieniona na ciepło a cześć zostanie zużyta do transportu stopu. Segmentowa konstrukcja ślimaków pozwala kontrolować charakterystyki przetwarzania poprzez dopasowanie geometrii ślimaków do zadania.
Wolna objętość w sekcji procesu jest związana ze stosunkiem Do/Di, który jest definiowany jako średnica zewnętrzna (Do) podzielona przez średnicę wewnętrzną (Di) ślimaka. Głębsze przeloty skutkują większą wolną objętością i niższymi średnimi szybkościami ścinania, ale mniejszym momentem obrotowym, ponieważ średnica wałów ślimaków będzie mniejsza. Większa wolna objętość oznacza większą głębokość kanału, która skutkuje większą różnicą temperatur. Różnica temperatur w kanale dotyczy temperatury przy ścianie cylindra i przy rdzeniu ślimaków.
Modele wytłaczarek LE-2CC 2x20 mm oraz LE-2CC 2x24 mm mogą być wyposażone w układy uplastyczniające, które są zamienne i współpracują z tą samą przekładnią o wartości Do/Di=1,60 oraz Do/Di=1,80. W przypadku stosunku Do/Di 1,80/1 średnia temperatura stopu będzie niższa ze względu na niższy pobór energii właściwej (kWh) na 1kg przetworzonego materiału i mieszanie. Efektem jest łagodniejsza/średnia geometria ślimaka. Stosunek Do/Di 1,80/1 pozwala na podanie większej ilości materiału do wytłaczarki. Osiągalny wzrost szybkości podawania materiału będzie porównywalny do wzrostu wolnej objętości związanej z wyższymi stosunkami Do/Di. Przy wyższych prędkościach ślimaka wzrost wydajności nie będzie tak wyraźny. W przypadku stosunku Do/Di 1,80/1 średnia temperatura topnienia będzie niższa ze względu na niższe zużycie energii właściwej (kWh) na 1kg przetworzonego materiału oraz łagodniejsze efekty mieszania związane z geometrią ślimaków.
Porównanie współczynników średnic i głębokości kanału ślimaków w wytłaczarce dwuślimakowej
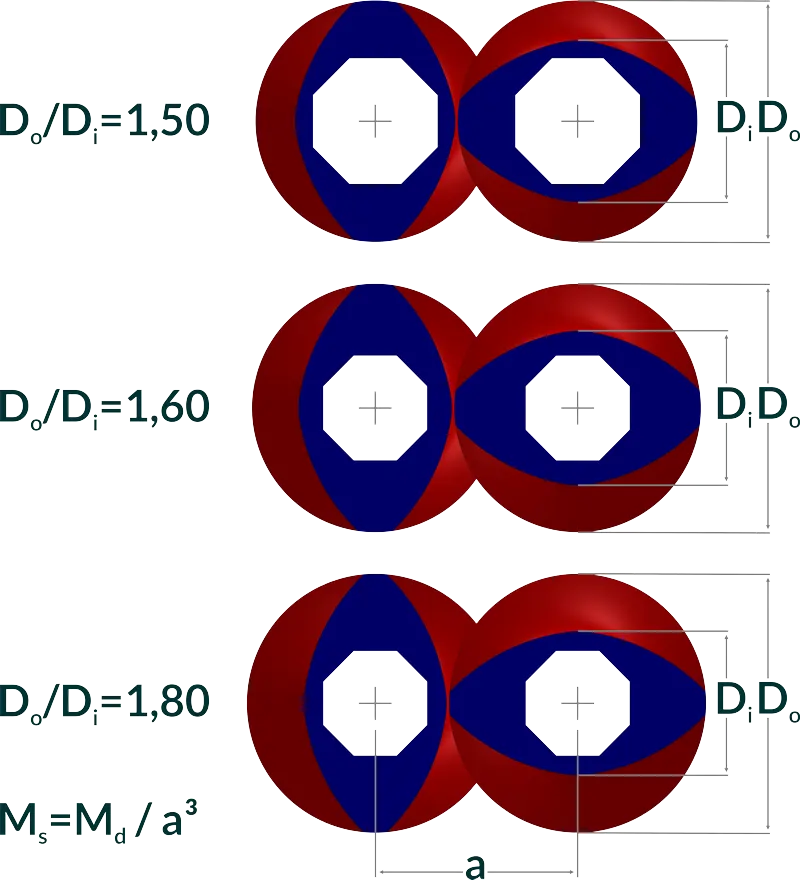
Rys.1 Porównanie współczynników średnic i głębokości kanału ślimaków w wytłaczarce dwuślimakowej.
Jak wyraźnie widać na ilustracji (Rys.1), dostępna przestrzeń w przekroju ślimaka na wał przenoszący moment obrotowy jest większa w przypadku wariantu geometrii Do/Di=1,50. W przypadku żywic o wysokiej energii przetwarzania, takich jak tworzywa termoplastyczne do zastosowań inżynieryjnych, daje to znaczące korzyści pod względem mocy, którą można zastosować do tych materiałów. Tworzywa termoplastyczne o wyższej energii wymagają do wytłaczania wysokiego momentu obrotowego ślimaków. Natomiast w przypadku Do/Di=1,80 występuje największa wolna objętość ślimaka.
Głębokość kanału ślimaków – wpływ na mieszanie ścinające i rozciągające.
Przy danej prędkości ślimaka w wypełnionym kanale można obliczyć średnią szybkość ścinania, przy czym ślimaki Do/Di = 1,80 mają niższą szybkość ścinania. Jako regułę można przyjąć, że szybkość ścinania przy 300 obr./min w wytłaczarce Do/Di = 1,60 jest taka sama jak w wytłaczarce Do/Di = 1,80 pracującej przy 500 obr./min. W rzeczywistości jednak te teoretyczne ograniczenia rzadko utrzymują się niezależnie od geometrii wytłaczarki i zazwyczaj można je przezwyciężyć, optymalizując warunki przetwarzania i konstrukcję ślimaka. Efektywne mieszanie wykorzystuje równowagę przepływów ścinających i rozciągających. Ekstruder dwuślimakowy, gdy kanały stają się pełne, ma zmianę objętości w kanałach przekroju poprzecznego między ślimakami, które zwiększają i zmniejszają objętość, gdy ślimaki się obracają. Te siły ściskania powodują serię naprzemiennych przepływów rozciągających do tyłu i do przodu wzdłuż ślimaków. W miarę jak stopień wypełnienia kanału wzrasta do 100%, stają się one bardziej intensywne. W miarę jak stopień wypełnienia wzrasta, intensywność przepływu wzrasta. Praca wykonana przez sprężanie i rozszerzanie materiału w blokach ugniatających jest proporcjonalna do iloczynu objętości i współczynnika sprężania. Połączenie tych efektów pokazuje znaczącą zaletę geometrii Do/Di = 1,80, która w tym przypadku ma większe objętości przepływu podłużnego. Ta analiza nie bierze pod uwagę prędkości roboczej ślimaka. Jeśli, co jest prawdopodobne, geometria wytłaczarki Do/Di = 1,80 może być efektywnie obsługiwana przy wyższych prędkościach ślimaka, ten efekt będzie jeszcze większy.
Wytłaczarki o średnicach ślimaków: 2x20 mm oraz 2x24 mm.
- Wytłaczarki LE-2CC 2x20 mm LE-2CC 2x24 mm mogą pracować jako współbieżne oraz po zmianie trybu pracy jako przeciwbieżne o zakresie długość cylindra L/D do 48.
- Wytłaczanie dwuślimakowe współbieżne jest stosowane głównie w procesach mieszania tworzyw, napełniana, odgazowywania czy wytłaczania reaktywnego. W wytłaczarce dwuślimakowej współbieżnej tworzywo przepływa z jednego ślimaka na drugi i przemieszcza się wzdłuż linii mającej kształt ósemki dzięki czemu droga tworzywa w cylindrze jest wydłużona i co zatem idzie czas przebywania również jest wydłużony. Ponadto w szczelinie między ślimakami wytłaczarki występuje ruch przeciwbieżny w wyniku, którego są w tym obszarze generowane duże naprężenia ścinające. Dlatego też, ten sposób wytłaczania znajduje zastosowanie w wielu procesach przetwórstwa tworzyw termoplastycznych.
- Wytłaczanie dwuślimakowe przeciwbieżne, zapewnia dobre karmienie wytłaczarki tworzywem zwłaszcza w przypadku materiałów w postaci proszku czy tworzyw wykazujących właściwości poślizgu. W porównaniu z wytłaczarką współbieżną krótszy i mniej zróżnicowany jest czas pobytu cząstek polimeru w cylindrze wytłaczarki. Przepływ tworzywa w wytłaczarce dwuślimakowej przeciwbieżnej jest całkowicie inny niż przepływ w wytłaczarce dwuślimakowej współbieżnej. Kluczowym czynnikiem tego przepływu jest podobny do działania pompy tzw. mechanizm wyporu, który nie występuje w innych rodzajach wytłaczarek. Stopień występowania mechanizmu wyporu zależy od stopnia zazębienia ślimaków wytłaczarki. Występuje w przypadku wytłaczarek przeciwbieżnych ściśle zazębiających się. Nie występuje tutaj przepływ wleczony.
- Kluczowym czynnikiem decydującym, o jakości i wiarygodności badań nad procesem wytłaczania jest kontrola i wiarygodny pomiar temperatury stopu w każdej ze stref wytłaczarki.
- Cylinder wytłaczarki jest dzielony wzdłuż osi podłużnej w celu uzyskania możliwości optycznej kontroli procesu uplastyczniania i mieszania stopu.
- Cylinder wytłaczarki jest wyposażony w porty dla dozowników bocznych oraz porty w górnej części cylindra do dozowania płynów lub gazów. Grzałki są rozmieszczone w taki sposób, aby ciepło było rozprowadzane równomiernie w każdej strefie grzewczo chłodzącej cylindra wytłaczarki.
- Czujniki mierzące temperaturę są rozmieszczone w taki sposób, aby zapewniać wiarygodny pomiar temperatury i ograniczać zakłócenia pomiaru pochodzące od grzałek pracujących w wyższej temperaturze niż układ uplastyczniający.
- Aby uniknąć niekontrolowanych wzrostów temperatury każda strefa cylindra jest wyposażona w wydajny i szybki układ chłodzenia, który współpracuje z układem grzania cylindra wytłaczarki tworzyw sztucznych.
- Precyzyjną kontrolę temperatury układu uplastyczniającego wytłaczarki zapewnia wielostrefowy regulator temperatury zaprojektowany przez naszą firmę.
- Układ sterowania temperaturą posiada możliwość kalibracji i kształtowania charakterystyki ogrzewania i chłodzenia układu uplastyczniającego przez badacza.
- Zaprojektowaliśmy cylindry z wymiennymi wkładkami stanowiącymi powierzchnię roboczą cylindra wytłaczarki. W praktyce oznacza to, że możemy poprzez wymianę wkładek cylindra w ciągu krótkiego czasu przystosować wytłaczarkę do pracy z innymi materiałami. Wymienne wkładki pozwalają na szybką i relatywnie tanią regeneracje układu uplastyczniającego. Wkładki w zasadzie mogą być wykonane z dowolnego materiału i w technologii, która się nadaje do tego celu. Komplet ślimaków jest łatwy do wymiany na inny. Można prowadzić badania nad praktycznie wszystkimi materiałami obejmującymi przemysł tworzyw sztucznych, medyczny, farmaceutyczny oraz materiałów ceramicznych.
- Wytłaczarki z przekładnią Vertex II zastępują dwie wytłaczarki, rozszerzając możliwości prowadzenia badań. Nasze wytłaczarki są wyposażone w przekładnie rozdzielającą moment obrotowy, które mogą pracować, jako współbieżne oraz przeciwbieżne, zmiana kierunku wirowania jest dokonywana automatyczne z pulpitu operatora.
- Wytłaczarki badawczeSitech3D mogą być wyposażone w precyzyjny tensometryczny pomiar siły działającej na ślimaki wzdłuż, mechanizm ten dodatkowo rozszerza możliwości prowadzenia badań. To opcjonalne wyposażenie wytłaczarek dwuślimakowych pozwala na pomiar sił osiowych działających na ślimaki na skutek działania ciśnienia w cylindrze wytłaczarki oraz odziaływania sił adhezji pomiędzy wytłaczanym tworzywem a ślimakami i cylindrem.
- Wytłaczarki z przekładnią Vertex II zastępują dwie wytłaczarki, rozszerzając możliwości prowadzenia badań. Nasze wytłaczarki są wyposażone w przekładnie rozdzielającą moment obrotowy, które mogą pracować, jako współbieżne oraz przeciwbieżne, zmiana kierunku wirowania jest dokonywana automatyczne z pulpitu operatora.
Dzięki starannemu projektowaniu oraz zastosowaniu materiałów i podzespołów wysokiej jakości nasze wytłaczarki badawcze są wiarygodne i powtarzalne zwłaszcza w zakresie parametrów mechanicznych, termicznych oraz systemów pomiarowych i dozowania. Wytłaczarki gwarantują krótki czas konieczny do wyczyszczenia i przygotowania do kolejnych badań. W praktyce laboratorium badawczego spełnienie takiego wymagania oznacza, że w krótkim czasie wytłaczarka musi osiągnąć i ustabilizować zadane przez naukowca parametry pracy, dotyczy to czasu nagrzewania i chłodzenia oraz co jest niezwykle ważne system ogrzewania i chłodzenia cylindra musi umożliwiać szybkie zmiany temperatury w górę i w dół w czasie trwania procesu. Nasze wytłaczarki laboratoryjne umożliwiają zmianę temperatury cylindra w górę w tempie ok 0,2 oC /s a w dół w tempie ok 0,12 oC/s. Wysokie tempo zmian temperatury powoduje, że wytłaczarka reaguje na zmiany dokonywane przez operatora w czasie zbliżonym do rzeczywistego. Zmiany zadanych parametrów są wiarygodne, powtarzalne i szybkie. Wszystkie dane pomiarowe są wiarygodne i rejestrowane w odstępach czasu zdefiniowanych przez użytkownika. Najkrótszy czas pomiędzy zapisami danych wynosi 1s dzięki czemu system pomiarowy może dostarczać bardzo dużych ilości danych, które mogą być analizowane i wizualizowane za pomocą takich popularnych narzędzi jak Excel.
Nasze laboratoryjne wytłaczarki dwuślimakowe LE-2CC 2x20 mm LE-2CC 2x24 mm oferują elastyczne konfiguracje od małych partii do produkcji w skali pilotażowej i doskonale nadają się do badań i rozwoju w sektorach polimerów, farmacji, biologii i nanotechnologii. Nasze wytłaczarki laboratoryjne spełniają szeroki zakres wymagań procesowych nawet w przypadku najtrudniejszych preparatów.
Celem zastosowania opisanych rozwiązań zastosowanych w wytłaczarkach dwuślimakowych jest uzyskanie możliwości prowadzenia badań na dowolnych tworzywach termoplastycznych, polimerach oraz innych materiałach w dużym zakresie temperatur oraz momentów obrotowych ślimaków. Wydajny system grzania i chłodzenia układu uplastyczniającego w połączeniu z możliwościami szybkiego otwarcia i czyszczenia cylindra oraz ślimaków pozwala na dostosowanie wytłaczarki do konkretnego zadania w krótkim czasie. Wytłaczarka szybko reaguje na zmianę temperatur poprzez operatora. Bogate wyposażenie dodatkowe oraz możliwość zmiany konfiguracji dodatkowo rozszerzają możliwości prowadzenia badań.
Ważne cechy użytkowe wytłaczarek dwuślimakowych laboratoryjnych LE-2CC 2x20 mm LE-2CC 2x24 mm.
- Duży zakres możliwości prowadzenia badań laboratoryjnych.
- Praca współbieżna przy zastosowaniu segmentowych ślimaków do pracy współbieżnej.
- Praca przeciwbieżna przy zastosowaniu segmentowych ślimaków do pracy przeciwbieżnej.
- Wysoki moment obrotowy ślimaków wytłaczarki oraz gęstość mocy.
- Wysoki zakres obrotów ślimaków wytłaczarki.
- Pomiar siły osiowej działającej na ślimaki.
- Cylinder wytłaczarki dzielony i otwierany wzdłuż osi poziomej.
- Wymienne wkładki cylindra stanowiące powierzchnię roboczą cylindra w celu łatwej regeneracji i możliwości zmiany materiału, z którego są wykonane.
- Możliwość zmiany położenia podajników bocznych bez konieczności demontażu cylindra (cecha unikalna, wymaga dodatkowego wyposażenia).
- Wysokie dopuszczalne ciśnienie wewnątrz cylindra wytłaczarki.
- Dedykowane dozowniki boczne sterowane przez komputer PLC wytłaczarki.
- Współpraca z systemami dozowania grawimetrycznego granulatów, proszków i płynów oraz gazów.
- Wydajny i ekonomiczny strefowy system grzewczo – chłodzący cylindra wytłaczarki.
- Niskie zużycie energii w trakcie pracy wytłaczarki.
- Ergonomiczna obsługa, bogate wyposażenie dodatkowe.
- Gabaryty urządzenia dostosowane do warunków laboratorium.
- Zaawansowane oprogramowanie badawcze.
- Obsługa naszych wytłaczarek podczas użytkowania i konserwacji jest łatwa na skutek zastosowania przemyślanych i zoptymalizowanych rozwiązań technicznych.
- Interfejs użytkownika jest przejrzysty i przyjazny. Stosujemy wygodne ekrany dotykowe, cyfrowe systemy sterowania PLC.
- Zdalne bezprzewodowe sterowanie z tabletu umożliwia kontrolę urządzenia w przypadku długo trwających procesów np. wytłaczania z bardzo niskimi prędkościami obrotowymi ślimaków.
- Dzięki zdalnej konserwacji Twoja wytłaczarka może się z nami połączyć. Kiedy potrzebujesz pomocy technicznej, inżynier może uzyskać dostęp do sterownika i od razu zająć się tym, co należy zrobić, np. dokonać aktualizacji oprogramowania wytłaczarki, bez konieczności podróżowania.
- Autonomiczny wodny i ciśnieniowy system chłodzenia strefy karmienia wyposażony we własną chłodnicę wody.
- Modułowa konstrukcja wytłaczarki laboratoryjnej pozwala na zmianę konfiguracji w trakcie użytkowania.
Zastosowanie wytłaczarek laboratoryjnych dwuślimakowych LE-2CC 2x20 mm LE-2CC 2x24 mm.
Te niewielkie wytłaczarki laboratoryjne o dużej mocy i dużych możliwościach przetwórczych przeznaczone do pracy z wymagającymi materiałami termoplastycznymi w warunkach laboratorium umożliwiają.
- Wytłaczanie praktycznie wszystkich dostępnych polimerów oraz innych plastycznych i termoplastycznych materiałów.
- Wytłaczanie polimerów napełnianych dodatkami mineralnymi, włóknami, proszkami metali, innymi wymagających dużych momentów obrotowych ślimaków.
- Wytłaczanie reaktywne wytłaczarki stabilnie pracują z prędkością ślimaków na poziomie 5 obr./min oraz mogą być skonfigurowane do pracy z prędkościami poniżej 1 obr./min dzięki czemu możliwe jest uzyskanie wydłużonych czasów przebywania materiału w cylindrze wytłaczarki.
- Wytłaczanie preparatów medycznych dzięki możliwości wymiany wkładek cylindra na wykonane ze stali kwasoodpornej np. AISI 440C lub stali o podobnych właściwościach.
- Wytłaczanie preparatów farmaceutycznych podobnie jak medycznych, często wymagane jest zastosowanie oprogramowania dostosowanego do wymagań produkcji farmaceutycznej.
- Wytłaczanie materiałów kompozytowych dzięki możliwości zastosowania dozowników bocznych, systemów odgazowania, dozowania oraz wydłużonych cylindrów owartości L/D=48.
- Wytłaczanie żywności jest możliwe dzięki możliwości zastosowania temperowanych termicznie matryc TVP (Textured Vegetable Protein) oraz kwasoodpornych wkładek do cylindra.
Wytłaczarki laboratoryjne służą pogłębianiu zrozumienia możliwości procesu wytłaczania jako podstawowego procesu przetwarzania tworzyw sztucznych, żywności oraz innych materiałów plastycznych.
W świecie nauki i produkcji, gdzie królują innowacja i wydajność, ewoluowały różne techniki i procesy, aby sprostać wymaganiom różnych gałęzi przemysłu. Wśród nich wyróżnia się wytłaczanie jako podstawowa i wszechstronna metoda stosowana w produkcji wielu przedmiotów codziennego użytku, od rur i przewodów po produkty spożywcze, a nawet filamenty do druku 3D. W swej istocie wytłaczanie jest procesem produkcyjnym polegającym na kształtowaniu surowców w profil o pożądanym przekroju poprzecznym za pomocą matrycy. Technika ta rozciąga się na tworzywa sztuczne, produkty spożywcze, metale, ceramikę i co czyni ją wszechobecną metodą przetwarzania w wielu gałęziach przemysłu. W procesie wytłaczania surowiec poddawany jest zagęszczaniu, ścinaniu, mieszaniu, napełnianiu, zmniejszaniu wielkości cząstek, przejściu fazowym i rozpadowi molekularnemu na skutek ścinania, które powstaje w wyniku działania ślimaków i tarcia cząstek materiału o siebie. Tak więc materiał po wejściu do cylindra wytłaczarki (układ uplastyczniający) zmienia się w postać stopioną dzięki wysokiemu ciśnieniu, wysokiej temperaturze i ścinaniu. Stop ten jest ostatecznie wytłaczany przez matrycę na końcu ślimaka i cylindra wytłaczarki, aby uzyskać pożądany kształt. Temperatura wewnętrzna zmienia się w zależności od rodzaju przetwarzanego polimeru lub mieszaniny polimerów i dodatków. Kiedy tworzywo sztuczne jest wytłaczane z matrycy, jest ono poddawane procesowi ochłodzenia, w którym czynnikiem chłodzącym może być powietrze lub woda. Zakresy zastosowań wytłaczarek laboratoryjnych powiększają się na skutek doskonalenia konstrukcji oraz wyposażenia oraz ważnej cechy, którą posiadają a mianowicie wytłaczarki umożliwiają pracę w sposób ciągły. Jeżeli zastąpimy np. reaktor zbiornikowy reaktorem w postaci wytłaczarki to będzie możliwa praca ciągła oraz modyfikowanie parametrów procesu w trakcie jego trwania dzięki małej objętości układu uplastyczniającego wytłaczarki, który będzie pracował jako reaktor przepływowy. Ponadto taki układ szybko reaguje na zmiany temperatury, obrotów ślimaków, zmiany dozowania składników a możliwości mieszania, rozcierania, ugniatania materiału są inne i zarazem większe niż w reaktorze zbiornikowym.
Odgazowanie cylindra ważny system wytłaczarki oraz operacja wymagana przy mieszaniu polimerów w celu uzyskania pożądanych właściwości chemicznych i fizycznych.
Odgazowanie jest jedną z kilku operacji wymaganych przy łączeniu (mieszaniu) polimerów między sobą oraz z dodatkami i wypełniaczami w celu uzyskania pożądanych właściwości chemicznych fizycznych. Powstały związek w postaci granulatu musi być wolny od pustych przestrzeni i resztkowych substancji lotnych. W przypadku polimerów higroskopijnych które są podatne na hydrolizę lub degradację masy cząsteczkowej w wyniku obecności wilgoci, skuteczne odpowietrzanie podczas mieszania ma kluczowe znaczenie dla osiągnięcia akceptowalnych właściwości fizycznych.
Otwory wentylacyjne w cylindrze wytłaczarki mogą pracować pod ciśnieniem atmosferycznym lub pod próżnią, w zależności od wymagań procesu. Większość typowych procesów mieszania obejmuje oba typy odpowietrzania. Wytłaczarki mogą być wyposażone w wiele otworów odpowietrzających do usuwania dużych ilości pary wodnej, rozpuszczalników lub monomerów, jednocześnie zapewniając niski poziom resztkowych substancji lotnych w gotowym produkcie. Opracowano różnorodne konstrukcje otworów wentylacyjnych dla współbieżnych wytłaczarek dwuślimakowych, aby dostosować się do szerokiego zakresu zastosowań i materiałów; obejmują one otwory wentylacyjne w górnej lub(i) bocznej części cylindra wytłaczarki. Każdy z tych projektów ewoluował, aby przezwyciężyć pewne problemy związane ze standardowymi konstrukcjami otworów wentylacyjnych, które znajdują się na górze cylindra wytłaczarki. Warunkiem stabilnej pracy systemów odgazowania, zarówno atmosferycznych, jak i próżniowych, jest niski stopień wypełnienia ślimaków w strefach odgazowania oraz bariera wysokiego ciśnienia (wypełniony stopionym polimerem ślimak) przed otworem wentylacyjnym.
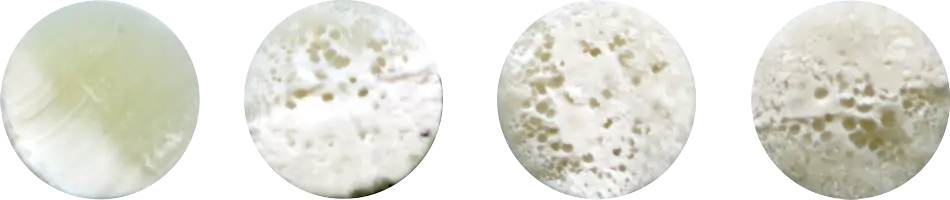
Rys.2 Efekt pracy systemu odgazowania cylindra wytłaczarki, po lewej stronie prawidłowo odgazowany stop, po prawej efekt wytłaczania bez odgazowania.
Problemy z wentylacją cylindra wytłaczarki można podzielić na dwie kategorie.
- Problemy operacyjne, w wyniku których polimer (lub/i inny surowiec) wydostaje się z otworów wentylacyjnych wytłaczarki. To zakłócenie procesu zwykle wymaga interwencji operatora w celu udrożnienia otworów wentylacyjnych.
- Resztkowe substancje lotne/gazy pozostają w mieszanym polimerze w wyniku niewystarczającego odgazowania cylindra wytłaczarki. W takim przypadku należy poprawić wydajność odpowietrzania poprzez zmianę konfiguracji ślimaków i cylindra wytłaczarki, aby uzyskać akceptowalną jakość produktu.
Każdy z tych problemów ma unikalne rozwiązania, jak opisano poniżej.
- Stop polimerowy wychodzi z otworu wentylacyjnego ekstrudera. Ta kategoria problemów jest powszechna w przypadku wszystkich wytłaczarek dwuślimakowych. Otwory atmosferyczne służą do uwalniania powietrza, wilgoci i innych lotnych gazów po początkowym stopieniu polimerów. Prędkość powietrza lub/i oparów wypływających z tych otworów wentylacyjnych jest funkcją objętościowego natężenia przepływu i otwartej powierzchni wentylacyjnej. Gdy prędkość gazu jest zbyt duża w wyniku zbyt dużej objętości lub zbyt małej otwartej przestrzeni, przepływające przez otwór gazy będą miały tendencję do porywania ciał stałych, co spowoduje wydostawanie się stopu przez otwór wentylacyjny. Rozwiązaniem jest zapewnienie zwiększonej powierzchni wentylacyjnej, co może wymagać skorzystania z dodatkowych otworów wentylacyjnych.
- Otwory atmosferyczne są wymagane w przypadku bocznego podawania wypełniaczy w postaci cząstek (talku, wypełniaczy mineralnych, CaCO3.) do stopionego polimeru. Otwory te mają za zadanie odprowadzać powietrze, które dostaje się do cylindra poprzez boczny podajnik razem z proszkami. Im mniejsza jest gęstość nasypowa wypełniacza, tym więcej powietrza wprowadza się do cylindra wytłaczarki, które należy usunąć. Jeśli powierzchnia otwarcia otworu wentylacyjnego jest zbyt mała w stosunku do objętości powietrza, które należy usunąć, wynikająca z tego duża prędkość wylotowa będzie miała tendencję do przenoszenia drobnych cząstek i proszku do otworu wentylacyjnego. Rozwiązanie tego problemu wymaga powiększenia obszaru wentylacyjnego poprzez dodanie dodatkowych otworów wentylacyjnych.
- Obecność niestopionego polimeru w strefie pierwszego podajnika bocznego powoduje również wydobywanie się wypełniacza z otworu odgazowania atmosferycznego powiązanego z tym bocznym podajnikiem. Aby zdiagnozować czy to jest przyczyną problemu, należy przeprowadzić fizyczną kontrolę jakości stopu w strefie otworu odgazowania tego podajnika bocznego, aby sprawdzić, czy obecna jest niestopiona żywica. W takim przypadku rozwiązanie wymaga modyfikacji konstrukcji ślimaka w części, w której topi się polimer przed otworem odgazowującym.
- Otwory odgazowania próżniowego są zwykle umieszczone w pobliżu głowicy i są zaprojektowane tak, aby uwalniać wszelkie resztkowe opary w warunkach próżni. Częstym problemem jest wypływanie stopu z tego otworu wentylacyjnego i jego blokowanie. Kiedy to nastąpi, gazy nie są usuwane ze stopionego materiału, a wytłoczyna staje się porowata i zawiera puste przestrzenie. Zablokowanie odpowietrznika wymaga ręcznego udrożnienia przez operatora. Istnieje kilka możliwych przyczyn i rozwiązań tego problemu:
- Stop może przedostawać się do otworu podciśnieniowego bezpośrednio w wyniku zwiększonej długości strefy ślimaka potrzebnej do wytworzenia wymaganego ciśnienia).
Gdy ciśnienie na sicie lub matrycy wzrasta, długość strefy ślimaka potrzebna do wytworzenia wymaganego ciśnienia odpowiednio się zwiększa, aż do osiągnięcia otworu odpowietrzającego w cylindrze wytłaczarki. Stop będzie wypływał w sposób ciągły z otworu wentylacyjnego, nawet bez podciśnienia. Rozwiązaniem tego problemu jest zmniejszenie ciśnienia w matrycy, zwiększenie długości strefy pompowania wytłaczarki poprzez przesunięcie otworu próżniowego o jedną strefę od głowicy lub dodanie strefy cylindra za otworem odgazowania próżniowego. Można też zainstalować pompę stopu w celu zapewnienia ciśnienia w głowicy i uwolnienia wytłaczarki od tego zadania. Ten sam stan wystąpi w przypadku zużycia elementów ślimaka w strefie pompującej na końcu cylindra wytłaczarki.
- Stop będzie również wypływał z otworu podciśnieniowego, jeżeli ciśnienie uszczelnienia ze stopionego polimeru jest mniejsze niż ciśnienie podciśnienia. Stan ten powoduje wyciąganie stopionego polimeru z cylindra wytłaczarki, ponieważ pompa próżniowa będzie wtedy zasysała powietrze przez cylinder wytłaczarki wraz polimerem. Wskazówką, że to jest przyczyna problemu, jest obserwacja wakuometru (próżniomierza). Jeśli wskaźnik nie zmienia się w czasie, oznacza to, że układ próżniowy jest szczelnie zamknięty. Jeśli widzisz wzrost ciśnienia, oznacza to, że przez układ przepływa duża ilość powietrza a otwór odgazowania będzie wypełniał się stopionym plastikiem. Jeśli stop wypływa z otworu podciśnieniowego dopiero po zastosowaniu podciśnienia, jest to objaw tego, że uszczelnienie ślimaka stopionym polimerem jest niewystarczające. Rozwiązaniem jest zmiana konfiguracji segmentów ślimaków w celu zastosowania bardziej restrykcyjnych elementów budujących ciśnienie.
- Należy wspomnieć o tym, że istnieją materiały termoplastyczne, które wykazują unikalne właściwości po poddaniu ich oddziaływaniu niskiego ciśnienia w wysokiej temperaturze. Takie materiały mają tendencję do zwiększania objętości i pienienia po dotarciu do strefy odgazowania i nie będą łatwo spływać z powrotem do ślimaków. Takie materiały wydostaną się z cylindra w każdych warunkach, jeśli używane są konwencjonalne otwarte otwory wentylacyjne. Materiały te można przetwarzać przy użyciu mechanicznych systemów dwuślimakowych zapobiegających rozszerzaniu się stopu poza cylinder wytłaczarki, a jednocześnie umożliwiają przepływ gazów wzdłuż ślimaków systemu mechanicznego odgazowania, który jest zainstalowany w otworze odpowietrzającym od góry lub boku cylindra. Systemy odgazowania mechanicznego podobne są w swojej konstrukcji do podajników bocznych, lecz maja krótsze ślimaki. Do tego celu może być wykorzystany masz podajnik boczny o po zmianie cylindra i ślimaków na co pozwala jego modułowa konstrukcja.
- Odgazowanie stopu można zwiększyć jeszcze w następujący sposób.
- Jeśli czas przebywania stopu w próżni jest czynnikiem ograniczającym (ograniczona dyfuzja), jedną z opcji jest zmniejszenie wydajności w celu wydłużenia średniego czasu przebywania.
- Inne rozwiązanie wydłużające czas przebywania wymaga wydłużenia stref odgazowania kosztem pozostałych stref i dokonania zmiany konfiguracji ślimaków, aby je dostosować do tych zmian.
- Zwiększenie poziomu podciśnienia poprzez zastosowanie innej pompy próżniowej.
- Zmniejszenie stopnia wypełnienia stopem polimeru strefy odgazowania poprzez zwiększenie skoku transportowych segmentów ślimaków. Mniejsze wypełnienie kanału ślimaków tworzy cieńsze warstwy stopu i ułatwia dyfundowanie gazu.
- Zmiana konfiguracji cylindra poprzez dodanie dodatkowych otworów wentylacyjnych. Może to wymagać wydłużenia cylindra w celu dodania dodatkowego otworu wentylacyjnego, jeśli w istniejącym nie ma wystarczającej ilości L/D. Cylindry laboratoryjnych wytłaczarek SiTEch3D standardowo maja długość L/D=40 i mogą mieć maksymalnie dziewięć otworów wentylacyjnych w górnej części cylindra i trzy w bocznej części cylindra. Natomiast cylindry wytłaczarek o długości L/D=48 i mogą mieć maksymalnie jedenaście otworów wentylacyjnych w górnej części cylindra i cztery w bocznej części cylindra. Położenie bocznych otworów można zmieniać bez konieczności demontażu całego cylindra.
Zastosowanie wytłaczarek laboratoryjnych w systemach współwytłaczania lub pracy kaskadowej.
- Proces współwytłaczania (koekstruzji) tworzyw sztucznych polega na wytłaczaniu dwóch lub więcej materiałów przez pojedynczą matrycę, tak aby materiały łączyły się w jedną strukturę przed schłodzeniem. Zaletą stosowania współwytłaczania jest to, że każdy zastosowany materiał zachowuje swoje pożądane charakterystyczne właściwości (takie jak sztywność, nieprzepuszczalność lub odporność na środowisko), których nie można byłoby osiągnąć w przypadku żadnego pojedynczego materiału polimerowego. W procesie współwytłaczania konieczne jest zastosowanie wielu wytłaczarek. Badania nad zrozumieniem mechaniki, zastosowań wytłaczania oraz nad nowymi materiałami będącymi mieszaninami i kompozytami polimerów zwłaszcza tych biodegradowalnych rzuca światło na znaczenie wytłaczania w nowoczesnej produkcji. W miarę postępu technologii wytłaczania i wzrostu zapotrzebowania na zrównoważone procesy produkcyjne badania procesów wytłaczania będą kontynuowane, przyczyniając się do powstania bardziej wydajnego, innowacyjnego i świadomego ekologicznie krajobrazu przemysłowego.
- Wytłaczarka kaskadowa przeznaczona do badań nad materiałami pochodzącymi z recyklingu lub innych, które mają nieregularne kształty, postać płatków lub pasty, które dodatkowo mogą być zabrudzone, zadrukowane, i o podwyższonej wilgotności noże wymagać zastosowania układu kaskadowego do karmienia wytłaczarki dwuślimakowej. Dodatkowa wytłaczarka kaskadowa zapewnia odpowiednią wstępną homogenizację i zagęszczenie materiału. Stop polimeru wychodzący z wytłaczarki wstępnej wprowadzany jest do strefy karmienia wytłaczarki dwuślimakowej. Kaskadowe elementy wytłaczane uzupełniają naszą ofertę produktów w zakresie produkcji wytłaczarek. Projektujemy, produkujemy i montujemy elementy kaskadowe wytłaczania do końcowego zastosowania. Składają się one zasadniczo z dwóch wytłaczarek – wytłaczarki do topienia i wytłaczarki do homogenizacji i ewentualnego odgazowania stopu. Powodem stosowania elementów wytłaczania kaskadowego jest oddzielenie etapów procesu topienia i homogenizacji, co pozwala na lepszą optymalizację poszczególnych etapów procesu. Zastosowanie układu kaskadowego wytłaczarek pozwala również uzyskać wydłużony czas przebywania stopu u układzie uplastyczniającym.
- Nasze wytłaczarki laboratoryjne to małe, wszechstronne urządzenia. Ich zadaniem jest ograniczone wykorzystanie materiałów, aby osiągnąć znaczące rezultaty badań. Dlatego doskonale nadają się do opracowywania produktów, pobierania próbek materiałów i produkcji małych partii produktów. Naszymi klientami są instytucje badawcze i uczelnie, producenci wyrobów z tworzyw sztucznych i firmy chemiczne. Podstawową konstrukcję można rozszerzyć o wiele wariantów wyposażenia oraz konstrukcje specjalne, aby sprostać indywidualnym wymaganiom klienta. Konstrukcja wytłaczarek o konstrukcji modułowej i nie modułowej oparta jest o innowacyjne założenia konstrukcyjne nowoczesne komponenty i jest oparta o wieloletnie doświadczenie zebrane w przemyśle przetwórstwa tworzyw.
Celem zastosowania opisanych rozwiązań zastosowanych w wytłaczarkach dwuślimakowych jest uzyskanie możliwości prowadzenia badań na dowolnych tworzywach termoplastycznych, polimerach oraz innych materiałach w dużym zakresie temperatur oraz momentów obrotowych ślimaków. Wydajny system grzania i chłodzenia układu uplastyczniającego w połączeniu z możliwościami szybkiego otwarcia i czyszczenia cylindra oraz ślimaków pozwala na dostosowanie wytłaczarki do konkretnego zadania w krótkim czasie. Wytłaczarka szybko reaguje na zmianę temperatur poprzez operatora. Bogate wyposażenie dodatkowe oraz możliwość zmiany konfiguracji dodatkowo rozszerzają możliwości prowadzenia badań.
|