Linie do produkcji filamentu stosowanego w druku 3D za pomocą technologii addytywnej.
Technologia druku 3D, często określana jako produkcja addytywna, jest stosowana w wielu branżach, coraz więcej firm stosuje tę przyszłościową technologię. Produkcja addytywna ma ogromny potencjał dla łańcuchów dostaw, rozwoju produktów i umożliwia tworzenie nowych modeli biznesowych.
Produkcja addytywna to specyficzny proces drukowania 3D. Ten proces polega na konstruowaniu części warstwa po warstwie poprzez osadzanie tworzywa zgodnie z cyfrowymi danymi projektowymi 3D. Termin „druk 3D” jest coraz częściej używany jako synonim wytwarzania przyrostowego. Jednak „wytwarzanie addytywne” lepiej odzwierciedla profesjonalny proces produkcyjny, który znacznie różni się od konwencjonalnych, ubytkowych metod wytwarzania. Na przykład, zamiast frezowania przedmiotu obrabianego z litego bloku, wytwarzanie przyrostowe buduje część warstwa po warstwie z materiału dostarczanego w postaci filamentu. W procesie drukowania 3D można stosować różne tworzywa sztuczne i materiały kompozytowe.
Produkcja addytywna ma zastosowanie w wielu dziedzinach oraz gałęziach przemysłu. Niezależnie od tego, czy jest wykorzystywana do budowy wizualnych i funkcjonalnych prototypów, czy małych i średnich serii i coraz częściej do produkcji seryjnej. Ta metoda oferuje przekonujące korzyści, których nie można osiągnąć konwencjonalnymi metodami. Rozwój produktu i wejście na rynek można znacznie przyspieszyć, a zwinne dostosowanie produktu i integrację funkcjonalną można osiągnąć szybciej i niższym kosztem. W ten sposób wytwarzanie addytywne daje dużym producentom z wielu różnych branż możliwość wyróżnienia się na rynku pod względem korzyści dla klientów, potencjału redukcji kosztów i celów w zakresie zrównoważonego rozwoju.
Największą zaletą przemysłowego druku 3D jest swoboda projektowania części, która nie zależy od żadnego narzędzia ani formy.
Produkt jest tworzony przez drukarkę 3D warstwa po warstwie z danych CAD 3D. Zmniejsza to koszty, zasoby i nakłady czasowe w wielu obszarach wykraczających poza produkcję wielkoseryjną. Prototypy można budować szybko i tanio, aby zoptymalizować projekty i przyspieszyć cykle rozwojowe. Komponenty do produkcji jednostkowej lub seryjnej mogą być elastyczne projektowane i wykonywane na zamówienie.
Technologia druku 3D charakteryzuje się niemal nieograniczoną swobodą projektowania oraz znacznie skróconymi czasami projektowania, produkcji i dostaw. Koszty rozwoju i produkcji są również drastycznie obniżone. Części o mniejszej wadze i większej złożoności stają się możliwe do wykonania, a produkcja wymaga mniej materiału i minimalnych ilości narzędzi.
Dzięki wytwarzaniu przyrostowemu produkcja oparta na projektowaniu staje się rzeczywistością.
Przemysłowy druk 3D oznacza, że proces produkcyjny nie określa już złożoności komponentu, ale raczej pożądaną funkcjonalność i wygląd produktu. Złożone geometrie, takie jak trójwymiarowe struktury z podcięciami lub zagłębieniami, są zwykle niemożliwe do wyprodukowania przy użyciu konwencjonalnych technologii, takich jak frezowanie, toczenie lub odlewanie, lub są możliwe tylko przy nieproporcjonalnie wysokich kosztach.
Teraz każdy kształt, który można skonstruować w programie CAD 3D, można wyprodukować za pomocą technologii wytwarzania addytywnego. Nie ma prawie żadnych ograniczeń nawet przy produkcji konstrukcji zawierających wewnętrzne puste przestrzenie. Jest to możliwe, ponieważ materiał jest dodawany przez drukarkę 3D tylko tam, gdzie powinien. Wytwarzanie addytywne daje projektantom nieograniczoną swobodę projektowania geometrycznego, a wysoka złożoność odgrywa tylko niewielką rolę w kosztach produkcji. Dzięki mniejszemu zużyciu materiałów często można nawet znacznie obniżyć koszty.
Drukowanie 3D za pomocą osadzania topionego tworzywa sztucznego (FDM).
Proces drukowania 3D FDM, znany również jako Fused Filament Fabrication (FFF), polega na rozwijaniu filamentu wyprodukowanego z tworzywa sztucznego ze szpuli i przetłaczaniu przez ogrzewaną dyszę głowicy drukarki 3D w kierunku poziomym i pionowym. Przedmiot jest tworzony natychmiast po stwardnieniu stopionego tworzywa sztucznego. Drukarka 3D wykorzystuje technologie ekstruzji stopionego tworzywa, wytłacza materiał przez dyszę głowicy na platformę roboczą, warstwa po warstwie.
Materiał do drukowania to filament wyprodukowany z tworzywa sztucznego nawinięty na szpule. Filament jest podawany do głowicy drukarki3D. Filament w głowicy drukarki jest podgrzewany, do momentu uzyskania odpowiedniej płynności następnie zostanie wytłoczony przez dyszę głowicy drukującej. Drukarka 3D wykorzystuje informacje z pliku cyfrowego. Projekt trójwymiarowy jest podzielony na wiele cienkich dwuwymiarowych przekrojów. Dzięki czemu drukarz dokładnie wie, gdzie umieścić stopione tworzywo sztuczne. Dysza głowicy drukarki 3D osadza stopiony polimer w cienkich warstwach, często o grubości 0,1 milimetra. Polimer szybko stygnie, wiążąc się z warstwą poniżej. Następnie platforma robocza drukarki 3D zmienia położenie o jedną warstwę drukowanego modelu, a głowica drukująca dodaje kolejną warstwę stopionego tworzywa. W zależności od wielkości i złożoności obiektu cały proces może zająć od kilku minut do kilku dni. Po zakończeniu drukowania modelu 3D obiekt wymaga odrobiny post-processingu. Może to obejmować odklejanie obiektu od platformy roboczej, usuwanie konstrukcji wsporczych.
Jeśli drukujesz za pomocą drukarki 3D w technologii FDM. Twoja drukarka 3D korzysta z wcześniej wyprodukowanego filamentu, który stopiony następnie układa warstwami na stole roboczym. Możesz mieć jedną z najlepszych drukarek 3D na rynku, użyć wszystkich odpowiednich ustawień drukarki 3D. Pomimo tego zakończyć proces niepowodzeniem wydruku lub brzydkim wydrukiem. Przyczyną niepowodzenia wydruku 3D będzie użycie odpowiedniego filamentu. Najlepsze filamenty do druku 3D mogą zapewnić dobrą przyczepność tworzywa do podłoża oraz uniknąć zatykania ekstrudera i w konsekwencji przerwania procesu druku 3D. Dobry filament pozwala budować modele o ostrych detalach i wysokiej wytrzymałości mechanicznej.
Jakość filamentu z tworzywa sztucznego stosowanego do druku 3D.
Właściwości mechaniczne i chemiczne filamentu znajdują odzwierciedlenie w cechach wydruku 3D. Nie można mieć złudzeń, złe właściwości filamentu odbiją się negatywnie na jakości wydrukowanego obiektu 3D. Co więcej, jeśli filament niskiej jakości zostanie zanieczyszczony, wzrasta ryzyko zakleszczenia ekstrudera drukarki 3D i przerwania druku.
Jakość filamentu do drukarek 3D można zmierzyć na podstawie odchylenia jego średnicy oraz owalności od wartości wymaganych. Jeśli średnica filamentu zmienia się szybko na małej odległości liniowej, prawdopodobnie zauważysz pewne niespójności na wydrukowanej ścianie modelu 3D, takie jak małe wybrzuszenia i wgłębienia. Może się tak zdarzyć, ponieważ drukarka 3D w jednym momencie wytłacza więcej stopionego tworzywa (podając filament o większej średnicy), a w innym momencie, gdy do głowicy wprowadzany jest filament o mniejszej średnicy, wytłacza mniej tworzywa. W skrajnych przypadkach, gdy średnica materiału jest zbyt duża, może on nie zmieścić się w wejściu ekstrudera i dojdzie do przerwania druku. Przerwanie druku modelu 3D jest kosztowne zwłaszcza w przypadku modeli drukowanych wiele godzin lub dni.
Drugim ważnym czynnikiem mającym wpływ na jakość filamentu jest obecność dużej inkluzji, która może doprowadzić do zablokowania dyszy głowicy drukarki i nieudanego drukowania. Natomiast obecność porowatości doprowadzi do powstania słabszych części, co jest ważne w bardziej zaawansowanych zastosowaniach.
Filament do drukarek 3D jest produkowany metoda wytłaczania stopionego polimeru lub kompozytu.
Do produkcji filamentu konieczne jest posiadanie odpowiednich urządzeń oraz znajomość procesu wytłaczania.
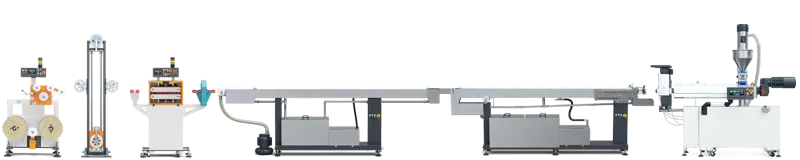
Rys.1 Linia do wytwarzania filamentu o wysokiej wydajności.
-
Linia jest dedykowana do produkcji filamentów z tworzyw termo topliwych przeznaczonych do zastosowania w drukarkach 3D.
-
Linia może być wykonana jako lewa lub prawa, co pozwala na ustawienie dwóch linii naprzeciwko siebie. W takiej konfiguracji ustawienia dwie linie mogą być obsługiwane przez 1 osobę.
-
Linia pozwala również produkować filament do innych zastosowań niż druk 3D np. do spawania tworzyw sztucznych.
-
Linia może być nadzorowana oraz serwisowana poprzez sieć Ethernet [Internet].
-
Linia może być sterowana bezprzewodowo z poziomu tabletu[opcja].
-
Linia może być konfigurowana i dostosowana do potrzeb klienta.
Opis urządzeń linii do produkcji filamentu przeznaczonego do do użycia w druku 3D.
-
Wytłaczarka filamentu zastosowana w linii do produkcji filamentu musi posiadać wysoką zdolność do wytłaczania z granulatu stopu o wysokiej jednorodności bez wtrąceń oraz pęcherzy.
Parametry takie jak prędkość obrotowa ślimaka, temperatury strefy karmienia, temperatury stref układu uplastyczniającego oraz wartości ciśnienia powinny być bardzo stabilne w długich okresach.
Wymaga to zastosowania w wytłaczarkach nowoczesnych napędów o wysokiej stabilności oraz pozwalających regulować prędkość obrotową ślimaka wytłaczarki w szerokim zakresie z zachowaniem stałego momentu obrotowego. Wymagania stawiane układom ogrzewającym i chłodzącym cylinder wytłaczarki również są wysokie. Należy dobrze zaprojektować cały system oraz zastosować dobrej jakości regulatory temperatury najlepiej w postaci sterownika przemysłowego PLC. Program sterowania powinien pozwalać na dostosowanie profilu termicznego wytłaczarki do prowadzonego procesu wytłaczania filamentu do drukarek 3D. Wytłaczarka filamentu powinna być przystosowana do łatwej i szybkiej wymiany ślimaka bez konieczności demontażu elementów linii.
Wytłaczarki do tworzyw sztucznych wyróżniają się wysoką wydajnością, trwałą budową, niskim zużyciem energii, a dodatkowo zajmują niewiele cennego miejsca.
Napęd ślimaka wytłaczarek filamentu do drukarek 3D.
Silnik napędowy ślimaka wytłaczarki pełni ważną rolę, ponieważ musi zapewnić bardzo stabilną prędkość obrotową ślimaka. Jest to ważne, ponieważ stabilne obroty ślimaka wytłaczarki zapewniają stabilne ciśnienie wytłaczanego tworzywa. Stabilność ciśnienia ma bezpośredni wpływ na stabilność średnicy filamentu. Do napędu ślimaków wytłaczarek w liniach do produkcji filamentu stosujemy nowoczesne silniki prądu przemiennego w technologii 120 Hz w zakresie mocy do 22kW. Takie silniki mają rozszerzony zakres stabilnego sterowania prędkością obrotową, zwłaszcza w zakresie niskich prędkości obrotowych oraz zapewniają stały maksymalny moment obrotowy w całym zakresie prędkości wirowania. Ważnym elementem układu napędowego ślimaka wytłaczarki jest przemiennik częstotliwości [falownik]. Dobrze dobrany falownik oraz odpowiednie oprogramowanie pozwalają na zapewnienie stabilnych obrotów ślimaka wytłaczarki w pełnym zakresie. Nasze napędy [silnik, falownik, program sterujący] zapewniają stabilną pracę wytłaczarki oraz oszczędzają energie elektryczną.
Łożysko oporowe ślimaka wytłaczarki filamentu.
Jest to kluczowy mechaniczny element konstrukcji wytłaczarki do filamentu. Parametry techniczne łożyska oporowego decydują o maksymalnym ciśnieniu pracy oraz o niezawodności i trwałości urządzenia. Łożysko oporowe musi pracować niezawodnie przy dużym obciążeniu wiele lat. Aby zapewnić niezawodną pracę łożysko w naszych wytłaczarkach jest smarowane olejem. Łożysko oporowe współpracuje bezpośrednio z motoreduktorem.
Moduł karmienia wytłaczarki granulatem tworzywa sztucznego.
Ważny podzespół wytłaczarki do filamentu, który ma wpływ na wydajność, jakość produktu, niezawodność, ergonomie pracy obsługi. Opracowany i zaprojektowany w naszej firmie moduł karmienia wytłaczarki jest przystosowany do pracy z granulatem lub proszkiem. Korpus modułu zasypu posiada wydajny system kanałów, poprzez które przepływa czynnik chłodzący. Wydajny wodny system chłodzenia strefy karmienia wytłaczarki zapobiega przedwczesnemu mięknięciu granulek tworzywa zapewniając stabilne pobieranie granulek. Analogicznie zapobiega sklejaniu się proszków. Stabilne pobieranie granulatu lub proszku jest ważne, ponieważ ma wpływ na stabilność ciśnienia oraz prawidłowe uplastycznienie tworzywa. Moduł karmienia wytłaczarki umożliwia łatwe opróżnienie i czyszczenie z granulatu lub proszku. Strefa karmienia wytłaczarki może być wyposażona w port do dozowania płynów oraz port do przedmuchiwania sprężonym powietrzem. Możliwe jest zainstalowanie dozowników grawimetrycznych oraz pneumatycznego systemu transportu granulatu. W przypadku zastosowania systemu suszenia granulatu tworzywa cały system dostarczania suchego granulatu jest hermetyczny. Jest to ważne, aby zapobiec przedostawaniu się wilgoci z powietrza do granulatu.
Układ uplastyczniający tworzywo zbudowany z cylindra i ślimaka wytłaczarki.
W procesie ekstruzji tworzyw sztucznych bardzo ważną rolę odgrywa układ uplastyczniający wytłaczarki zbudowany z cylindra oraz ślimaka, który stanowi kluczowy podzespół każdej wytłaczarki. Konkretny typ układu uplastyczniającego wytłaczarki dobierany jest adekwatnie do właściwości przetwarzanego tworzywa. Ślimak wytłaczarki odpowiada za jakość i konsystencję wytłaczanego tworzywa. W cylindrze wytłaczarki w wyniku ruchu obrotowego ślimaka materiał jest transportowany w kierunku głowicy. Tworzywo przemieszczające się w cylindrze wytłaczarki dostaje się do ogrzewanej strefy, gdzie ulega stopieniu, a następnie homogenizacji materiałowej i termicznej. Uplastyczniony i wymieszany stop podawany jest z odpowiednią wydajnością i z odpowiednim ciśnieniem do głowicy wytłaczarki, gdzie materiał jest formowany przyjmując kształt filamentu.
Układ uplastyczniający wytłaczarki spełnia cztery funkcje podstawowe:
-
nagrzewanie tworzywa, prowadzone w celu zapewnienia zadanego przebiegu zmian stanów fizycznych tworzywa przetwarzanego, określanego temperaturą. Strefowy system ogrzewania cylindra wytłaczarki ma za zadanie dostarczyć energii cieplnej koniecznej do prowadzenia procesu uplastycznienia tworzywa.
-
sprężanie mechanicznie tworzywa w celu usunięcia powietrza spomiędzy jego granulek. Następnie wytworzyć w stopionym tworzywie stabilne ciśnienie mające na celu uzyskanie zadanego przebiegu zmian ciśnienia.
-
mieszanie, zapewniające homogenizowanie, czyli ujednorodnienie składu i właściwości, głównie cieplnych i mechanicznych, jak również struktury tworzywa przetwarzanego oraz równomiernego w masie nagrzania stopu do wymaganej temperatury
-
transportowanie, umożliwiające przemieszczanie tworzywa przez układ z uzyskaniem na jego końcu potrzebnej prędkości wypływu tworzywa z określonym natężeniem i ustaloną fluktuacją oraz pulsacją.
Jakość projektu, wykonania oraz odpowiedni dobór komponentów układu uplastyczniającego mają bezpośredni wpływ na jakość wytłaczanego filamentu do druku 3D.
Cylinder jest wyposażony w zamknięcie klinowe pozwalające w łatwy sposób dołączyć głowicę lub pompę tworzywa. Cylinder zawsze jest wyposażony w osłonę zawierającą izolację termiczną wykonaną ze stali nierdzewnej, która ogranicza możliwość dotknięcia rozgrzanego cylindra przez obsługę oraz ogranicza straty ciepła.
Kluczowym elementem wyposażenia wytłaczarki do filamentów jest mechanizm obrotu układu uplastyczniającego [bez konieczności zmiany położenia wytłaczarki względem linii] w celu wymiany ślimaka lub konieczności jego wyczyszczenia. Mechanizm zapewnia powtarzalne ustawienie głowicy wytłaczarki względem linii a w szczególności względem kalibratora podciśnieniowego.
Termoregulacja stref cylindra wytłaczarki do filamentu.
Jeżeli chcemy produkować dobry filament do drukarek 3D to wytłaczarka powinna posiadać dobrej jakości układ uplastyczniający, stabilny układ napędowy ślimaka oraz co niezwykle ważne stabilny i dokładny system ogrzewania cylindra.
Ekologiczne termoregulatory, które stosujemy w naszych wytłaczarkach posiadają bardzo dobre parametry techniczne i jednocześnie są proste w obsłudze. Każda strefa z pięciu stref cylindra jest wyposażona w cyfrowy układ regulujący temperaturę w zakresie do 400 oC. Każda strefa cylindra wytłaczarki posiada grzałki elektryczne, które pozwalają w krótkim czasie uzyskać zadaną temperaturę oraz radiator z wentylatorem, pozwalający na szybkie obniżenie temperatury. Grzałki oraz układ chłodzenia są jednocześnie regulowane poprzez cyfrowy regulator PID (proporcjonalno całkująco różniczkujący). Takie rozwiązanie umożliwia utrzymanie zadanej temperatury stopu z dużą dokładnością ok 1 oC (pomiar temperatury jest dokonywany z dokładnością 0,1 oC). Cyfrowy system regulacji temperatury pozwala uniknąć tzw. przesterowań, czyli niekontrolowanych wzrostów lub obniżeń temperatury. Cyfrowy regulator temperatury opracowany przez nasz dział automatyki, nadzoruje pracę wszystkich stref wytłaczarki jednocześnie, uwzględniając ich wzajemne odziaływanie na siebie.
W linii do produkcji filamentu do drukarek 3D pomiędzy cylindrem wytłaczarki a głowicą jest zainstalowana pompa tworzywa z własnym precyzyjnym napędem oraz systemem ogrzewania. Zastosowanie pompy pozwala na poprawę stabilności przepływu i ciśnienia strumienia tworzywa dostarczanego do głowicy formującej filament. W trakcie pracy każdej wytłaczarki jednoślimakowej na skutek ruchu obrotowego ślimaka występuje niewielka pulsacja ciśnienia oraz ślimak wytłaczarki wprawia tworzywo w ruch obrotowy. Zastosowanie zębatej pompy tworzywa pozwala wyeliminować te zjawiska oraz pozwala precyzyjnie kontrolować prędkość liniową wytłaczanego filamentu.
Zastosowanie pompy umożliwia rozdzielenie procesu wytłaczania filamentu na dwa niezależne etapy.
-
Wytłaczarka odpowiada za uplastycznienie tworzywa, jeżeli jest wyposażona w pompę tworzywa nie musi budować ciśnienia, ponieważ za to odpowiada pompa. Jeżeli wytłaczarka filamentu nie musi budować wysokiego ciśnienia tworzywa to pozwala na sterowanie procesem uplastycznienia tworzywa w większym zakresie dając większe możliwości stosowania różnych receptur.
-
Pompa tworzywa pozwala na precyzyjną regulacje strumienia tworzywa dostarczanego do głowicy oraz ciśnienia wytłaczania filamentu niezależnie od parametrów pracy wytłaczarki. Zastosowanie pompy tworzywa poprawia parametry wytłaczania oraz rozszerza możliwości wytłaczarki.
Pompa jest wyposażona w takie same regulatory temperatury jak wytłaczarka. System sterowania wytłaczarki i pompy stopionego tworzywa jest zintegrowany i pozwala kontrolować obydwa urządzenia jednocześnie z jednego panelu dotykowego.
Pompa tworzywa jest zamontowana w linii do wytłaczania filamentu w sposób umożliwiający pracę linii z pompą oraz bez niej. Zmiana trybu pracy linii jest łatwa i nie wymaga specjalistycznych narzędzi.
3. Głowica wytłaczarki formująca wytłaczany filament.
Głowica formująca wytłaczany filament jest tym elementem linii, który w zależności od narzędzia formującego, ustala ostateczny kształt wytłaczanego filamentu. Wszystkie części głowicy mające kontakt ze stopionym tworzywem są poddane procesowi azotowania, co pozwala na uzyskanie dużej odporności na ścieranie. Głowica jest grzana grzałkami opaskowymi i są w niej umieszczone gniazda do podłączenia czujników temperatury oraz czujnika ciśnienia. Głowica również jest wyposażona w takie same regulatory temperatury jak wytłaczarka i pompa oraz jest sterowana z panelu dotykowego wytłaczarki.
Głowica jest mocowana do pompy tworzywa lub wytłaczarki za pomocą łatwego w obsłudze zamknięcia klinowego. Głowica formująca filament do drukarek 3D jest standardowo wyposażona w dwa narzędzia do wytwarzania filamentu o średnicach 1,75 mm i 2,85 mm. Dokładność średnicy wytłoczonego filamentu nie jest gorsza niż ±0,05 [mm]. Wymiana narzędzia jest łatwa i nie wymaga stosowania specjalistycznych narzędzi. Wszystkie elementy głowicy mające styczność z tworzywem są azotowane do twardości 1000oHV i na głębokość nie mniejszą niż 0,5 mm.
4. System chłodzenia wytłaczanego filamentu do drukarek 3d.
Wytłaczarka zastosowana w linii do produkcji filamentu oferuje standardowy zakres temperatur pracy od temperatury otoczenia do 400oC. Filamenty najczęściej są wytłaczane w zakresie temperatur od ok 160 do 300oC z wyjątkiem tworzyw termoplastycznych wysokotemperaturowych jak PEEK.
-
Wytłoczony filament należy schłodzić do temperatury otoczenia a przynajmniej do temperatury, w której nie będzie ulegał odkształceniom mechanicznym w trakcie procesu produkcji. Sprawa wydaje się prosta, przeciągamy filament przez zimna wodę i gotowe. Niewątpliwie większość produkowanych filamentów jest chłodzona za pomocą zimnej wody. Jednak chłodzenie stopionych tworzyw sztucznych ma wymagania technologiczne oraz ograniczenia, które wynikają z praw fizyki oraz właściwości tworzyw sztucznych.
-
Po pierwsze tworzywa sztuczne mają niskie przewodnictwo ciepła. Ten efekt powoduje, że ochłodzenie filamentu wymaga dużo czasu a w trakcie chłodzenia występuje duża różnica temperatur pomiędzy powierzchnią, która ma bezpośredni kontakt z woda a wnętrzem filamentu. Zjawisko narasta wraz ze wzrostem średnicy filamentu w sposób nie liniowy.
-
Po drugie nie wszystkie tworzywa dobrze tolerują gwałtowne chłodzenie zimną wodą. Pozna powiedzieć, że stopniowe chłodzenie zawsze jest lepsze, ponieważ ogranicza gwałtowny skurcz termiczny wytłaczanego tworzywa zmniejszając negatywne zjawiska z tym związane. Z tego powodu tworzywa często są wytłaczane do ciepłej lub gorącej wody. Ponadto niektóre tworzywa używane do produkcji filamentów dobrze zachowują owal jeżeli przed wejściem do wody przebywają w powietrzu, które chłodzi łagodniej niż woda.
Aby pogodzić te wymagania procesowe zaprojektowaliśmy i produkujemy wannę do chłodzenia wytłaczanego filamentu, która pozwala na ogrzewanie i chłodzenie wody w zakresie od 7 do 80 oC. Wanna jest wyposażona w bardzo precyzyjny mechanizm regulacji odległości wejścia filamentu do wody oraz w podciśnieniowy kalibrator średnicy filamentu.
Wanna do chłodzenia wytłaczanego filamentu z chłodzeniem oraz grzaniem wody.
Filament (żyłka) do druku 3D wytłaczany przez głowicę przechodzi do wanny z ciepłą lub gorącą wodą. Następuje w niej schładzanie wytłoczonego filamentu. Ciepła woda (temperatura w wannie w zależności od tworzywa wynosi od 40 do 80°C) zapobiega niekontrolowanemu i gwałtownemu skurczowi wytłaczanego filamentu.
Wanna ciepła jest wykonana ze stali kwasoodpornej i posiada mechanizm pozwalający na jej precyzyjny przesuw wzdłuż osi podłużnej. Układ przesuwu ułatwia pracę operatora dając możliwość odsunięcia wanny od głowicy na czas uruchamiania linii oraz zapewnia precyzyjną i zarazem powtarzalną regulacje odległości od głowicy wytłaczarki. Odległość ta jest zależna od rodzaju wytłaczanego tworzywa. Temperatura wody w wannie jest utrzymywana dzięki zespołowi czujników. Wanna pracuje w obiegu zamkniętym. Długość wanny wynosi ok. 3000 [mm], maksymalna temperatura wody wynosi 80 °C. Przesuw wanny możliwy jest w zakresie 200 mm. Wanna pracuje w układzie zamkniętego obiegu wody [rozwiązanie ekologiczne], który jest wyposażony w pompę obiegowa o regulowanej wydajności oraz tkaninowy łatwy w obsłudze filtr wody. Dopełnianie wody w zbiorniku odbywa się automatycznie. Zbiornik wody wyposażony jest w układ podgrzewania wody do wymaganej temperatury, potem ta temperatura jest stabilizowana. Wszystkie funkcje wanny są sterowane z poziomu panelu operatora.
Kluczowym elementem wanny ciepłej jest kalibrator, który powoduje, że filament jest jednego kształtu i średnicy. Kalibrator działając pod ciśnieniem, stabilizuje wymiar wytłaczanego filamentu i kontroluje, aby odchyłka średnicy nie przekraczała wartości +/- 0,05 mm. Kalibrator posiada wymienne ustniki o różnych średnicach oraz mechanizm regulacji położenia w dwóch osiach, który zapewnia możliwość jego precyzyjnego ustawienia względem głowicy wytłaczarki, co jest niezwykle ważnym czynnikiem, dla jakości filamentu. Ponadto kalibrator jest wyposażony w pompę podciśnienia z możliwością precyzyjnej regulacji.
Wanna do chłodzenia wytłaczanego filamentu.
Zadaniem wanny z zimną wodą jest ostateczne schłodzenie filamentu do druku 3D. Stała, niska temperatura wody pozwala na odprowadzenie ciepła z filamentu w efektywny sposób. Wanna pracuje w układzie zamkniętego obiegu wody [rozwiązanie ekologiczne], który jest wyposażony w pompę obiegowa o regulowanej wydajności oraz siatkowy łatwy w obsłudze filtr wody. Dopełnianie wody w zbiorniku odbywa się automatycznie. Zbiornik wody wyposażony jest w układ schładzania wody do wymaganej temperatury, potem ta temperatura jest stabilizowana. Wszystkie funkcje wanny są sterowane z poziomu panelu operatora. Wanna jest wykonana ze stali kwasoodpornej a w końcowej części wyposażona w osuszacz powietrzny. Temperatura wody w wannie jest utrzymywana dzięki zespołowi czujników temperatury. Długość wanny wynosi 3 000 [mm] . Minimalna temperatura wody w wannie zależy od temperatury wody zasilającej wymiennik ciepła. Aby uzyskać wysoką wydajność chłodzenia filamentu konieczne jest dostarczenie zimnej wody do systemy wymienników ciepła wanny z wytwornicy zimnej wody. Wanna nie jest standardowo wyposażona w wytwornice zimnej wody.
Wanna zimna jest wyposażona w dwa mechaniczne zgarniacze wody oraz wydajny osuszacz ciśnieniowy. Osuszacz jest tak zaprojektowany, aby nie wprawiał filamentu w drgania. Powietrze konieczne do pracy osuszacza jest dostarczane przez wentylator promieniowy. Zastosowanie wentylatora eliminuje konieczność dostarczania sprężonego powietrza, które jest drogie.
Do pomiaru średnicy filamentu w dwóch lub trzech osiach służy laserowy miernik z zintegrowanym wyświetlaczem pomiaru. Wyniki pomiaru mogą być wyświetlane na wyświetlaczu, w który jest wyposażony miernik oraz dodatkowo transmitowane do systemu sterowania linią i prezentowane w postaci graficznej ponadto system sterowania linią umożliwia zapis tych danych. Pomiar średnicy jest niezbędnym elementem w procesie produkcji filamentu.
Odciąg posiada gąsienice o długości kontaktu z wytłaczanym profilem 400 mm i szerokości 80 mm.
Linie do produkcji filamentu wyposażone w odciągi gąsienicowe przeznaczone do pracy ciągłej 24/7.
Kluczowym zagadnieniem mającym wpływ na jakość produkowanego filamentu jest stabilny transport liniowy. Stabilność prędkości liniowej produkowanego filamentu jest niezwykle istotna, ponieważ każda zmiana prędkości będzie skutkować zmianą średnicy filamentu. Jest to zależność, której nie można wyeliminować ani ograniczyć. Stabilny transport oznacza precyzyjne utrzymywanie zadanej prędkości liniowej wytłaczanego filamentu i jego średnicy.
Odciąg gąsienicowy jest rozwiązaniem sprawdzonym i uniwersalnym, ponieważ umożliwia transport profili o różnych przekrojach poprzecznych. Precyzyjne sterowanie prędkością liniową pozwala na bardzo dokładną regulację wymiarów filamentu. Odciąg gąsienicowy posiada gąsienice pokryte warstwą materiału, który zapewnia wysokie tarcie pomiędzy gąsienicą a filamentem. Stosowane materiały na pokrycie gąsienic to Corex lub Linatex - materiały o wysokiej odporności na zużycie ścierne.
W celu zapewnienia stabilnej prędkości liniowej odciągu gąsienicowego stosujemy niezależne napędy dla każdej z gąsienic.
Stosujemy dwa rodzaje napędów gąsienic odciągu:
-
Motoreduktory napędzane asynchronicznymi silnikami prądu przemiennego pracujące w technologii 120 HZ wyposażone w cyfrowe enkodery. Takie motoreduktory w połączeniu z nowoczesnymi falownikami pozwalają na utrzymanie stabilnej prędkości z zachowaniem nominalnej siły uciągu w zakresie 1 do 100. Jest to ważny parametr, ponieważ umożliwia regulacje prędkości linii np. zakresie od 1 m/min do 100 m/min lub do 2 m/min do 200 m/min.
-
Motoreduktory napędzane silnikami synchronicznymi prądu przemiennego (serwo) Takie motoreduktory w połączeniu z nowoczesnymi falownikami pozwalają na utrzymanie stabilnej prędkości z zachowaniem nominalnej siły uciągu w zakresie 1 do 1000. Jest to ważny parametr, ponieważ umożliwia regulacje prędkości linii np. zakresie od 0,1 m/min do 100 m/min lub do 0,2 m/min do 200 m/min. Takie napędy są jednak znacznie droższe.
Odciągi gąsienicowe są wyposażone we własny cyfrowy sterownik PLC oraz dotykowy panel operatora. Zastosowanie własnego sterownika PLC jest rozwiązaniem wygodnym dla obsługi oraz umożliwia prace odciągu jako urządzenie niezależne lub pracujące w linii produkującej filament do druku 3D. Odciągi są wyposażone w system bezpieczeństwa, który zabezpiecza przed niekontrolowanym dostępem w strefę ruchomych części.
W procesie produkcji filamentu konieczna jest wymiana szpul na które jest nawijany produkowany filament. Wymiana szpuli jest łatwa trwa ok 10-15 s i nie powoduje konieczności zaczynania produkcji filamentu.
Pionowy kompensator siły naciągu jest w istocie magazynem wytłaczanego filamentu, który odbiera wytłaczany filament w czasie wymiany szpuli na nawijarce dwuwrzecionowej. Kompensator pozwala operatorowi na łatwą zmianę szpuli bez konieczności przerywania procesu wytłaczania. Kompensator może zmagazynować 30 lub 40 m filamentu. Kluczowym wyposażeniem kompensatora jest zintegrowany laserowy miernik położenia rolek. Precyzyjny pomiar położenia rolek pozwala na precyzyjną współpracę magazynu z nawijarką eliminującą pulsację siły naciągu w procesie nawijania. Magazyn posiada możliwość regulacji siły naciągu filamentu w dużym zakresie poprzez system odpowiednio dobranych obciążników.
To niepozorne urządzenie spełnia kluczową role ponieważ pozwala wygodnie wymienić szpule w nawijarce filamentu oraz co niezwykle ważne dzięki wykorzystaniu praw fizyki oraz laserowego pomiaru odległości pozwala nawijarce utrzymywać stałą zaprogramowaną siłę naciągu filamentu w trakcie nawijania na szpule.
Produkowany filament do drukarek 3D należy zmagazynować. Ponieważ filament jest konfekcjonowany na niewielkie szpule stosowane w drukarkach 3D najłatwiej jest go magazynować również na szpulach o dużej pojemności. Dwuwrzecionowa nawijarka filamentu to urządzenie, które umożliwia nawijanie filamentu w ciągu technologicznym. Nawijarka jest przystosowana do nawijania filamentu na szpule o średnicy do 400 [mm] i szerokości do 500 [mm]. Duża pojemność szpul zmniejsza częstotliwość koniecznych zmian w trakcie produkcji filamentu. Mechanizm mocowania szpul wyposażony jest w łatwe w obsłudze zaciski. Nawijarka wyposażona jest w licznik długości nawiniętego filamentu oraz miernik siły naciągu. Szpule nawijarki napędzane są poprzez dwa nowoczesne niezależne napędy. Do właściwego układania żyłki na szpuli zastosowano układacz mechaniczny Uhing GmbH, który sprzężony jest z napędem szpuli. Nawijarka ściśle współpracuje z magazynem filamentu poprzez cyfrowy system sterowania zapewniając stabilny naciąg filamentu oraz funkcje magazynowania.
Wszystkie funkcje nawijarki są sterowane z niezależnego dotykowego panelu operatora wyposażonego w cyfrowy sterownik PLC. Dzięki temu urządzenie może pracować niezależnie lub w linii do produkcji filamentu. Zastosowanie ekranu dotykowego ułatwia obsługę, ponieważ operator nie jest zmuszony podchodzić do głównego panelu operatora.
9. Cyfrowy system sterowania linią do produkcji filamentu do drukarek 3D.
Na podstawie wielu lat doświadczeń, dział automatyki opracował oprogramowanie pozwalające na zarządzanie wytłaczarkami oraz liniami do produkcji filamentu. Nasze oprogramowanie pozwala sterować, kontrolować i zarządzać procesami wytłaczania filamentu.
Ciągła kontrola parametrów wytłaczania takich jak: ciśnienie, temperatura, obroty, moment obrotowy, zużycie energii, pozwalają kontrolować i sterować procesem i urządzeniami linii do produkcji filamentu.Można do tego dodać możliwość zapisu parametrów do bazy danych w celu późniejszej analizy i archiwizacji, wyświetlanie wykresów on-line oraz pracę w sieci zakładowej a nawet globalnej.
Nasze oprogramowanie możemy dostosować do oczekiwań naszych klientów. Proces można kontrolować z poziomu ekranu dotykowego na konsoli urządzenia lub w sieci Ethernet.
10. Wyposażenie dodatkowe linii do produkcji filamentu do drukarek 3D
-
Osuszacz surowca z podajnikiem pneumatycznym
Niektóre tworzywa sztuczne używane do produkcji filamentu do drukarek 3D wymagają starannego wysuszenia. Suszenie tworzyw, które chłoną wilgoć z powietrza jest konieczne, aby uzyskać filament bez pęcherzy pary wodnej, która w oczywisty sposób pogorszy właściwości filamentu. Do usunięcia wilgoci z granulek tworzywa sztucznego służą osuszacze różnych producentów, które możemy dostarczyć razem z naszymi liniami do produkcji filamentu. W przypadku zastosowania osuszacza granulek tworzywa nasze wytłaczarki wyposażamy w podciśnieniowy system transportu granulek z osuszacza do leja zasypowego wytłaczarki. Jest to rozwiązanie, które zapewnia szczelność całego układu karmienia wytłaczarki i eliminuje dostęp wilgotnego powietrza. W większości przypadków, osuszacz jest niezbędnym elementem linii do produkcji filamentu. Suszenie tworzywa do wytłaczania filamentu ogranicza radykalnie powstawanie pęcherzyków pary wodnej w wytłaczanym filamencie i wpływa korzystnie na stabilność wymiarową wytłaczanego filamentu.
Wytłaczarka linii do produkcji filamentu może być wyposażona w systemy dozowania, zapewniające podawanie ściśle określonych, zadanych ilości surowców do cylindra wytłaczarki.
W skład wyposażenia systemu dozowania mogą wchodzić następujące urządzenia:
- Adapter mocowania systemu dozowników do cylindra wytłaczarki, wyposażony w porty do dozowania płynów bezpośrednio na ślimaki oraz port do przedmuchiwania powietrzem lub gazem obojętnym.
- Mieszalnik statyczny przystosowany do montażu 2 dozowników na wytłaczarce, 1 szt.
- Dozownik grawimetryczny do proszków z mieszadłem MCPOWDER 0,2-16.4 kg/h, dla gęstości nasypowej 0,6 kg/dm3, zasobnik 5L.
- Dozownik Grawimetryczny do granulek 0,72-18 kg/h zasobnik ok 5L.
- Zasobnik główny bez dozowania 10 L
- Jednostka sterująca pracą dozowników współpracująca z ekranem dotykowym wyposażona w interfejs do komunikacji z linią do wytłaczania filamentu.
|